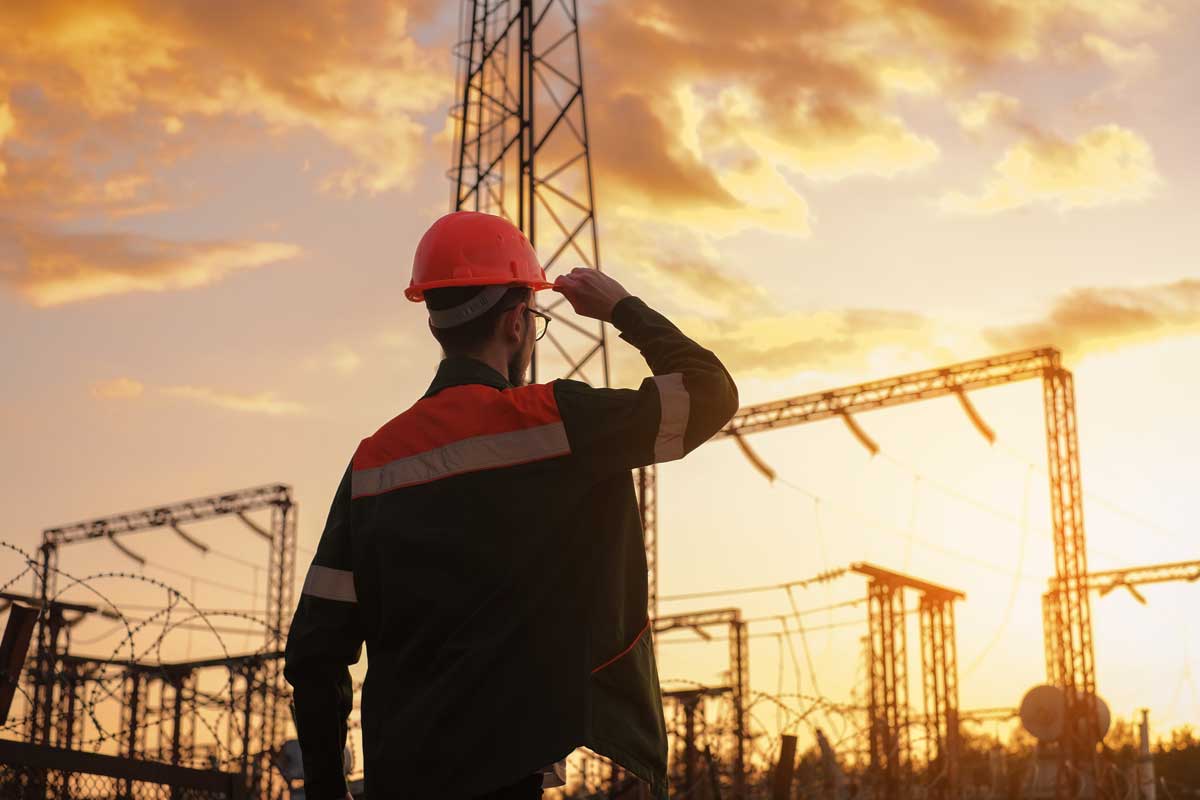
In all areas of electrical design and construction, wire splicing is a crucial part of building safe, robust, and efficient electrical systems. Sometimes it’s necessary to connect wires together, either to extend the circuit or to join different parts of a system together.
Wire splicing is simply the joining of two wires to complete an electrical path, generally to create a permanent connection. In today’s post, we will look at a few of the key things you need to know about wire splicing.
What Are the Main Types of Wire Splicing Methods, and How Do They Differ?
Today, there are three main types of wire splicing. The first is using solder, which is also the oldest method, dating back about 100 years, before the invention of crimping machines. This process involves melting lead solder throughout the connection to form the joint.
The second method is crimping, or using a tool to attach a connector to the wires. The splice connector is chosen based on its cable size, a color code marking, and a die number. Those details determine what type of crimping connector and tool are used.
The third type is shear bolt splicing. This involves adding a series of bolts onto a copper coupler, then tightening down on the bolt until the head snaps off. A splice typically uses four to six bolts. This is a reliable method that requires less skill than crimping.
Factors Influencing Wire Splicing Choice
The best method of splicing varies according to the voltage of the connection and the types of cables being used. There are two different types of electrical conductors used in electrical cables: copper and aluminum. It is vital to know what type of cable you are using, as this will determine what type of connector you should choose.
When deciding which type of splice to use, look for a die code number and a color code based on the cables that you are splicing together. For example, a 500 MCM will have a code and color unique to that specification.
Here at MAC, we also deal with extra high voltage splices, specifically high-pressure, fluid-filled cable splices. These types of splices are most often created with compression type connectors, or multi-RAM indent connectors. The latter involves indentors inside a copper sleeve that fits over the conductors to form the electrical connection.
When dealing with high or extra high voltage, you need to remove insulation and then reinsulate over the area for the splice, using more insulation than what was present initially. This additional insulation accounts for the non-factory-application conditions of the splice.
Key Challenges and Considerations
Wire splicing for non-low-voltage splices is not something that just anyone can do. It is a highly skilled process that follows a specific set of steps, and it should only be performed by trained individuals. Improperly spliced wires can lead to weak connections, increased electrical resistance, and potential safety hazards such as short circuits or electrical fires. The process of splicing can also be dangerous if you don’t take proper care.
Before beginning any wire splice, you must understand the type of cable that you have, the voltage, and the tools that you will require as well as the type of splice to use. It is also essential for safety considerations to have a clean work environment.
When you are dealing with extra high voltage systems or additional complicating factors, such as transitioning from the conductor in the center all the way to the outside surface, splices need to be constructed in a specific manner.
The area around a splice usually needs to remain straight for a certain distance; it is not advisable to bend a cable sharply near a splice as this can place undue stress upon the cable. There are exceptions, known as angle splices, but these are relatively uncommon.
Implementing Best Practices
Before splicing, it is essential to prepare properly and to select the correct splicing method. Always check with your splice manufacturer for the latest updates and newest technologies before you begin.
Follow proper splicing technique, and never allow an untrained person to perform a splice. Many manufacturers also offer training on how to perform a proper splice. If this is available, it is strongly recommended that you take advantage of it.
Insulation is vital, too. Spliced connections should be insulated properly to protect against moisture, corrosion, and other electrical hazards.
After splicing, test the connection thoroughly to ensure that it is safe and meets the expected performance requirements. Keep records of your splices, including the types of splice used and the results of any tests you have performed.
We recommend using color codes for dies, allowing you to more easily match the correct dies to the correct cables.
Learn More and Purchase Cable Splicing Kits and Accessories
Here at MAC Products, we are the leading supplier of extra high voltage splice kits. With ample inventory, excellent customer support, and the ability to splice different size cables together in various ways, we have become the go-to supplier for our clients over the past 40 years. We are also able to support customers with custom solutions.
We supply Complete Unit Splice Kits for an array of industries and applications in addition to manufacturing and offer a broad range of cable splicing accessories, including tapes, ground straps, solder, cable supports, insulating materials, and manhole hardware.
Our products are designed to be versatile and suitable for use in virtually any kind of installation, and each kit is customized for the exact cables that are being spliced together. And if you require a specific or hard-to-find component, we may be able to help you.
If you would like to learn more about any of our products or about any of the issues we have covered in today’s post, please feel free to contact us at any time. A member of our team will be happy to provide assistance.