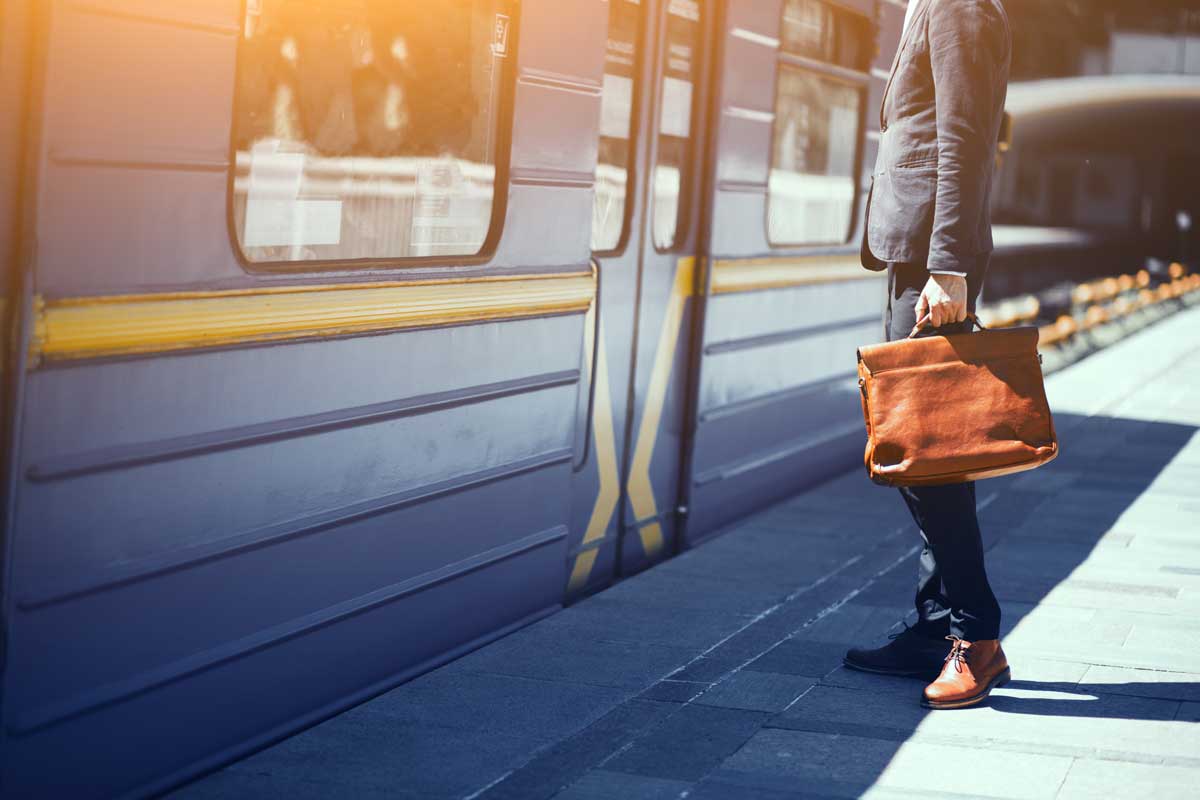
Mass transit is a crucial part of modern life, with millions of us relying upon it every day to commute to work, visit friends and family, and go about our lives. And in this age of ever-increasing consciousness of environmental issues, electrified transit is fast taking over the industry.
Though Americans make almost 10 billion journeys by public transit per year as of 2019 (source: APTA), most of us do not understand much—if anything—about how these systems work. Today we are going to take a close look at one type of electrified mass transit: the rigid catenary system (RCS).
The term “rigid catenary system” is a slight misnomer, as an RCS is not actually a catenary system in the strictest sense. It is a type of electrification system that is most commonly used for underground transit such as subways. Power is still collected by a pantograph and delivered to the vehicles, just as in an ordinary catenary system. However, this system doesn’t rely on tensioned wires. Instead, a large aluminum extrusion holds the wires in place by clamping the contact wire.
What Are the Advantages of Rigid Catenary Systems?
Rigid catenary systems offer a number of benefits when they are used appropriately. They require a lower system height, meaning that the clearance above the system is smaller than with a traditional flexible catenary. There is no mechanical tension on the wire in an RCS, which eliminates the hazard presented by tensioned wires.
There is also a power distribution advantage because an RCS provides a larger cross-sectional area for the current to flow through. Because there are fewer overall parts and pieces, there are fewer points of failure, making maintenance easier.
A rigid catenary system can be applied in highly specific situations in which other types of electrification may not be suitable. Examples include floating bridges and bridges that lift up or swing side to side. When a system has pivoting or moving structures that a track or vehicle has to travel through, a rigid catenary is far more useful than a traditional catenary.
Efficiency and Reliability Improvements
When used properly, rigid catenary systems can bring significant improvements in efficiency and reliability.
The large cross-sectional area of the extrusion in an RCS helps to make power distribution more efficient, while fewer overall components mean that maintenance is easier. Maintenance crews have fewer materials to bring out into the field when something breaks down or needs to be repaired, and there are fewer knock-on impacts in the event of a failure.
For example, if a wire wears too thin and snaps in a traditional catenary system, that will likely require a larger overall repair job. But since there is no tension in a rigid catenary system, a worn-out wire can be fixed by simply replacing the short section that is impacted. There will be no need to replace the surrounding clamps, hangers, and supports. This allows for a faster return to service and lowers maintenance costs.
Additionally, because a rigid catenary does not rely on applying tension to the wires, no post-installation adjustment to the system is required. In a traditional tensioned catenary system, the wire tends to “creep” because copper elongates slightly over time. Adjustments may need to be made several times over the course of a few years before a traditional system stabilizes itself.
Performance in Different Rail Applications and Environments
A rigid catenary system can be used almost anywhere. These systems are, in general, highly resistant to the impacts of polluted air, salty air, moisture, and high or low temperatures. However, they perform at their best when utilized in tunnels, bridges, and other low-clearance applications. Using an RCS in an open environment is likely to be extremely expensive, though. This is partly because an RCS requires more support points located more closely together than with a traditional catenary system.
Addressing Maintenance, Weather, Safety, and Other Challenges
As we have already discussed, fewer components and fewer materials mean that maintenance of an RCS is generally easier. Thanks to a system called “retractable catenary,” the energized bar can be powered down and then moved, giving personnel full access to the roof to perform repairs without the risk of electrocution.
Since rigid catenary systems are primarily utilized in tunnels, weather implications are rarely a concern. One common RCS accessory is a plastic shroud that sits over the catenary to divert water flow. This is useful in tunnels or any space in which water could drip through and deposit minerals on the catenary, impeding the current flow to the vehicles.
One common challenge of rigid catenary systems is speed restriction. Supports typically sit at 30-foot intervals, but the faster the train goes, the shorter that support interval gets. This means that an RCS comes with an inbuilt speed restriction of around 95 mph, though some may be able to go slightly faster under particular circumstances.
Another challenge is that the bars come in 12-meter (30-foot) lengths. This means that, when installing or replacing a bar, the length is limited for each piece. This is not the case in a traditional catenary system, in which the wire can be hung to any required length. RCS bars can be cut, but cannot be lengthened beyond 12 meters.
Learn More
MAC is one of the leading providers of rigid catenary system bars and all the parts and components that support them. We have worked on an array of RCS projects in environments such as tunnels, bridges, and under highways as well as in maintenance facilities. Some of our recent projects include the I-90 floating bridge in Seattle and the MBTA Green Line in the Boston area.
If you would like to learn more about any of our projects or any of the products and services we offer, please contact us today and a member of our team will be happy to advise you.
Related Posts
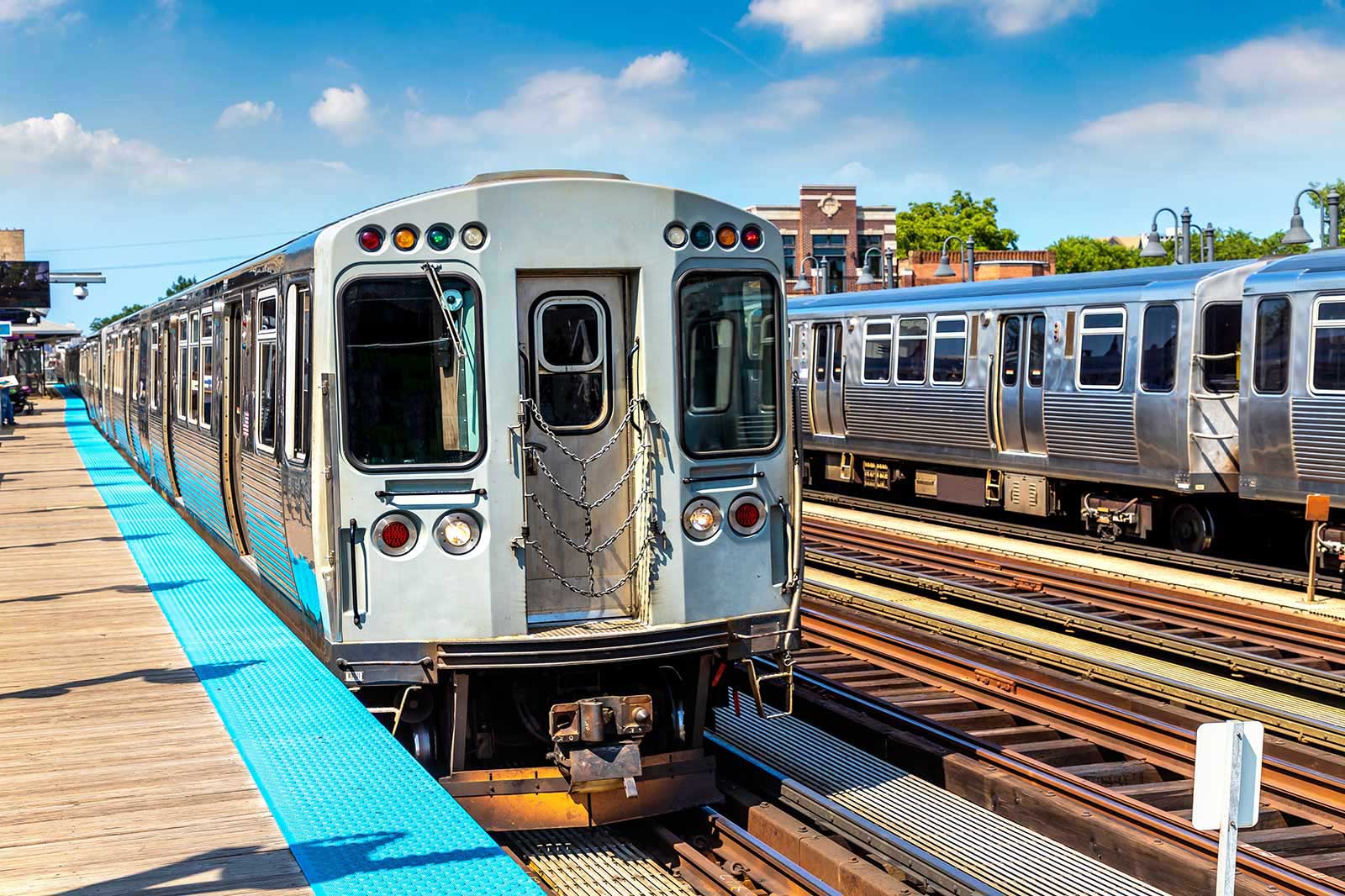
What Is a Third Rail System, and What Are Its Benefits?
Third rail systems are a common means of delivering power to trains. Learn more about what these types of systems are.