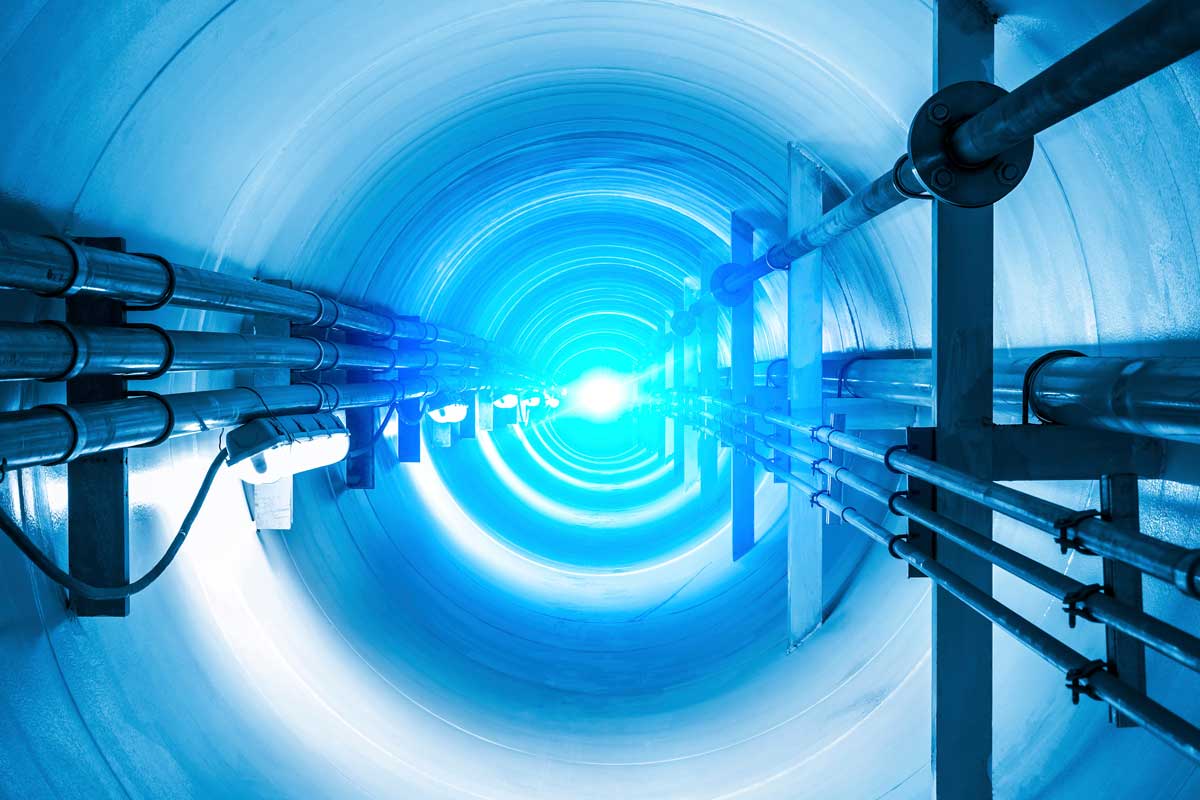
Pipe-type cables are used in many extra-high-voltage underground systems for the transmission of electrical power. They are an alternative to overhead cables and are ideal in situations where space is at a premium, such as in busy and densely populated towns and cities. Pipe-type cable systems have been in use since 1932 and are efficient, effective, safe, and low-maintenance.
You can read more about pipe-type cable systems in our recent blog post on this subject. Today, we wanted to take a closer look at one of the components that make up a pipe-type cable system: connectors.
Understanding Pipe-Type Cable Connectors
In electrical systems, it’s sometimes necessary to join two or more cables together to connect two circuits or to lengthen a circuit. In these situations, the conductors need to be spliced together in a safe and effective way.
Performing a splice like this necessitates using a connector, which mechanically joins the two pieces of cable and forms an electrical bridge between them.
Pipe-type cable connectors are custom-designed and fabricated as cylindrical ferrules (often made of copper). Conductors can then slide into both ends of the ferrule, and the connectors can be compressed to retain the conductors.
Applications of Pipe-Type Cable Connectors
Pipe-type cables are specifically used in the underground transmission of power, as opposed to overhead power solutions. Underground routing of cables for power transmission is typically required in urban settings.
They’re also useful in locations where lines can’t be routed overhead due to the interference they would cause or, in some cases, aesthetics. One common example of this is power transmission in and around airports.
Types of Pipe-Type Cable Connectors
There are three main types of connectors used for pipe-type cable systems. The first is the traditional copper connector, which is installed using machinery called a four-ram press. This tool uses four hardened indenter pins to compress the connector into the cable conductors so it stays firmly in place. These connectors are used in traditional pipe-type cables.
The second type is a bimetallic connector, used to join a copper cable to an aluminum cable. One half of the connector is copper and one half is aluminum, and these halves are factory-joined together in the middle. The connector is welded to the conductor on the aluminum side, and the copper side has a four ram press compression connector.
Finally, the third type of pipe-type cable connector is the field-machined connector, used in newer pipe-type cable systems that use laminated polypropylene paper (LPP) tape for insulation rather than standard kraft paper tape. Since this paper is stiffer, the connector needs to be crimped and formed differently than a four-ram press can manage. Typically, this means performing a full die compression and then using specialized equipment to create a curvature to the connector, making it easier to apply the splice tapes over the connector.
Factors to Consider When Choosing Pipe-Type Cable Connectors
Since there are multiple types of pipe-type cable connectors, it’s important to choose the optimal one for any given application. Several factors will go into this decision.
First of all, materials need to be considered. If you have a copper conductor, for example, then the cable will need to be made out of copper too. Likewise, if you have an aluminum cable, you’ll need an aluminum connector.
In choosing whether to use ram press traditional style connectors or their field-machined counterparts, you’ll need to consider the insulation that sits over that conductor. Aluminum conductors were once popular because they were cheaper than copper. However, newer-style LPP connectors have largely supplanted aluminum because it’s just not as good a conductor as copper.. Splicing an aluminum conductor is also more complex than a copper splice.
Best Practices for Installing Pipe-Type Cable Connectors
When it comes to installing pipe-type cable connectors, the most important thing is to have the right machinery and equipment. These systems require specialized equipment such as a four ram press—a hydraulic device with particular pin sizes that will compress the connector at the required depths. In addition, special dies and tools to compress the connector for LPP cables are also necessary.
Aluminum connectors are usually joined using welded connections. In this case, you’ll need a highly skilled welder. The conductor needs to be completely cleaned of any oil and debris before welding, as excess oil can result in a dirty weld that won’t provide a reliable connection.
Do Pipe–Type Cable Connectors Require Maintenance?
Pipe-type cable systems and their connectors require very little maintenance. Once the system is installed, it will be covered by insulation and then sealed up in a steel casing. If something does fail, either a joint will need to be rebuilt or it will need to be cut out so a new piece of cable can be spliced in.
Pipe-type cable systems, including connectors, are designed to last for 40 years. However, in reality, they can last for much longer than this. It’s not unusual for a pipe-type cable system to remain in place and functioning well for 80 years or more!
Learn More and Explore MAC’s Range of Pipe-Type Cable Connectors
MAC is proud to be the leading supplier of splice kits for pipe-type cable systems. These kits include everything you need to perform a splice, including the required connectors as well as tapes, braids, and casings.
Our complete product offering is not limited to a particular voltage or type of cable, so no matter your requirements, we can support you.
If you’d like to learn more about our products or any of the issues we’ve addressed in this post, please contact us, and a member of our team will be pleased to advise you.