Travel is an unavoidable part of modern life. Whether commuting to work, traveling to a different state to visit loved ones, or flying overseas for business or a vacation, the vast majority of people now use public transit at least occasionally. For many, it is part of daily life. In fact, Americans took 9.9 billion journeys by public transit in 2019 alone, according to APTA.
However, most people do not understand how those mass transit vehicles work. Here at MAC Products, we play a key role in the electrified transport industry, providing high-quality accessories used across an array of systems.
Today, we’re going to offer a closer look at one important type of public transport: catenary electric railways.
What Is a Catenary System?
A catenary system uses an overhead wire to supply electricity to vehicles such as light rail trains and streetcars.
Catenary systems are an alternative to third rail systems for electrified transit. They are primarily used for overground transit. Some underground transportation networks do also use this approach, though there is a significant difference between overhead and underground system requirements and structures.
How Overhead Catenary Systems Work
A catenary system uses two wires: the catenary wire and the contact wire. As a vehicle passes by, the pantograph (an apparatus mounted on the roof of the vehicle to collect power) makes contact with the latter, using this friction to collect the electricity. The catenary wire then feeds electricity to the vehicle via the pantograph, powering the vehicle. Current flows through the vehicle and back to the feeder station via the steel wheels on the running rails.
Catenary systems can be powered in two ways: direct current (DC) and alternating current (AC). A DC power catenary system, usually between 600 and 1,500 volts, is primarily used in urban and local transportation environments. An AC catenary system is usually 25kv and is most often used for regional train lines.
There are two main types of catenary systems. An overhead catenary system (OCS) consists of tensioned wires that are somewhat flexible. As a train passes by, these suspended wires move up and down. An overhead conductor rail (OCR) system, also sometimes called the rigid system, utilizes a rigid bar held between supports. This holds the wire that the pantograph interacts with.
What Is the Structure of an Overhead Catenary System?
Overhead catenary system components all follow the same basic principles but can be constructed in slightly varying ways. Most notably, there are several ways to support the overhead wires in a catenary structure.
One common option is to position a pole next to the track where a cantilever system holds the wires in place suspended above the track. Another way is to create a portal structure with a rectangular gateway, out of which a structure extends to support the wires. In a tunnel, the wires can be suspended from the ceiling.
Wires are hung at a specific tension, and the catenary wire is connected to the contact wire at regular intervals, held in place by connectors and clamps. Insulators are also placed between the catenary wires and the support structure. This prevents the surrounding structure from becoming energized, which can be dangerous.
How Much Power Is Needed for Catenary Systems?
How much power is in overhead train lines depends on the type of catenary system. The catenary wire’s power is fed from a traction power substation (TPSS). For a local DC-powered light rail system, the power required ranges from 1 to 4 megawatts; for an AC system, the power required ranges from 20 to 100 megawatts.
What Are the Benefits of a Catenary System?
As the negative impact of fossil fuels on the environment and the catastrophic implications of climate change become more widely understood, governments and transit authorities are continually searching for more sustainable and environmentally friendly alternatives. Electrified transit is a far greener way to travel. In addition, mass electrified transportation reduces congestion and pollution in our cities.
Compared to a third rail system (the other most common form of electrified transit), catenary systems are likely safer. Because the overhead wires are out of reach, there is little to no chance of somebody inadvertently touching the electrified part of the system.
Catenary systems are comparatively less expensive to build, particularly for intercity and long-distance travel where a third rail system would be too costly. Catenary railways can also reach much higher speeds.
What Types of Catenary Systems Are Best for Different Transportation Types?
Different types of catenary systems are appropriate for different types of transportation. Light rail and streetcars in urban areas, for example, are generally DC powered, while high-speed and long-distance rail uses the 25kv AC system.
In the instance of trolley buses, which, unlike the other types of transit mentioned, do not have running rails, the catenary system works slightly differently. There are two upward-extending poles at the back of the bus connecting to two overhead wires via a grooved collector shoe. One of these wires is positively charged, and the other negatively, completing the circuit and powering the bus.
Future Opportunities for Catenary Systems
In addition to their current uses in mass public transit, catenary systems represent exciting potential in two other significant areas: trucking and mining.
Many companies, including those in Europe and China, are considering the possibilities of curbing freight emissions (a major source of pollution in many areas) by moving freight trucks to an electrified overhead catenary system. This would involve dedicated lanes with overhead wires installed on which electrified trucks can run.
The difference between this and rail-based catenary systems is that the trucks could also disconnect from the electrified wires and run on their independent internal engines where necessary.
In some areas, mines have also considered the possibility of both installing an OCS and making these systems driverless. For example, the company ABB has developed a system known as eMine™ with various solutions such as enabling mining vehicles to run on an electric trolley assist line, eliminating the need for diesel fuel. This was implemented at Copper Mountain Mining in British Columbia, Canada, in 2021.
What You Need to Know About Catenary System Maintenance
In general, once catenary systems are up and running, they tend to be fairly low maintenance. Catenary construction is robust, and the infrastructure can last 20 to 40 years before needing a significant overhaul.
One common issue with catenary wires often occurs when the system is new: Copper wire has a tendency to creep to its full extended length before it settles, meaning that maintenance teams may need to adjust it manually to ensure it is correctly positioned. In addition, at the end of the wire run, the balance weight that creates tension on the wire may need to be readjusted, particularly in very hot or very cold weather.
Any aspect of the catenary system with a movable part will need to be greased occasionally to keep it in good working order. It is also essential to keep a close eye on the insulators for damage, since they can be harmed by cold or heat.
While catenary systems are generally robust enough to handle most weather conditions, extremely cold weather can cause a layer of ice to form along the contact wire, where the pantograph collects its power. Simple preventative measures, such as spraying the wires with a de-icer or adding a scraper to the pantograph to chip away the ice, can mitigate this issue to a large extent. Another option, known as CAT Heat, involves attaching another wire to the top of the contact wire, allowing the wire to heat up and prevent it from freezing.
Learn More
Here at MAC, we design and manufacture numerous components used in OCS cantilever assemblies. As a leading overhead catenary system supplier, we design, manufacture, and supply everything from the poles outward. We also manufacture products that make up part of the rolling stock, and we supply pole-mounted sectionalizing switches as well as pad-mounted and wall-mounted switches.
In addition, we are involved in the maintenance facilities or depots for these systems, supplying equipment to help transit authorities perform the required routine maintenance on rail cars.
We are also at the forefront of developing these systems and exploring new and creative ways of using them to solve contemporary transit problems. For example, in Seattle, Washington, a floating bridge on the I-90 over Lake Washington is currently under construction. When it is complete, trains will traverse this bridge.
We have played a major role in this exciting development by designing a unique OCS-OCR expansion joint system, which works with the bridge’s multidirectional movements in response to the lake’s water level. The expansion joint is unique because it needs to be tension-free so it does not affect the bridge pontoon’s movement, while creating a naturally smooth curvature for the train’s pantograph to maintain good contact and power transfer. A full-scale mockup test was performed in Pueblo, Colorado, with excellent results.
If you would like to learn more about any aspects of rail electrification or overhead catenary systems, or if we can assist you with supplies, support, consulting, or maintenance, we would love to hear from you. Please get in touch with a member of our team, and we’ll be happy to advise you.
Related Posts
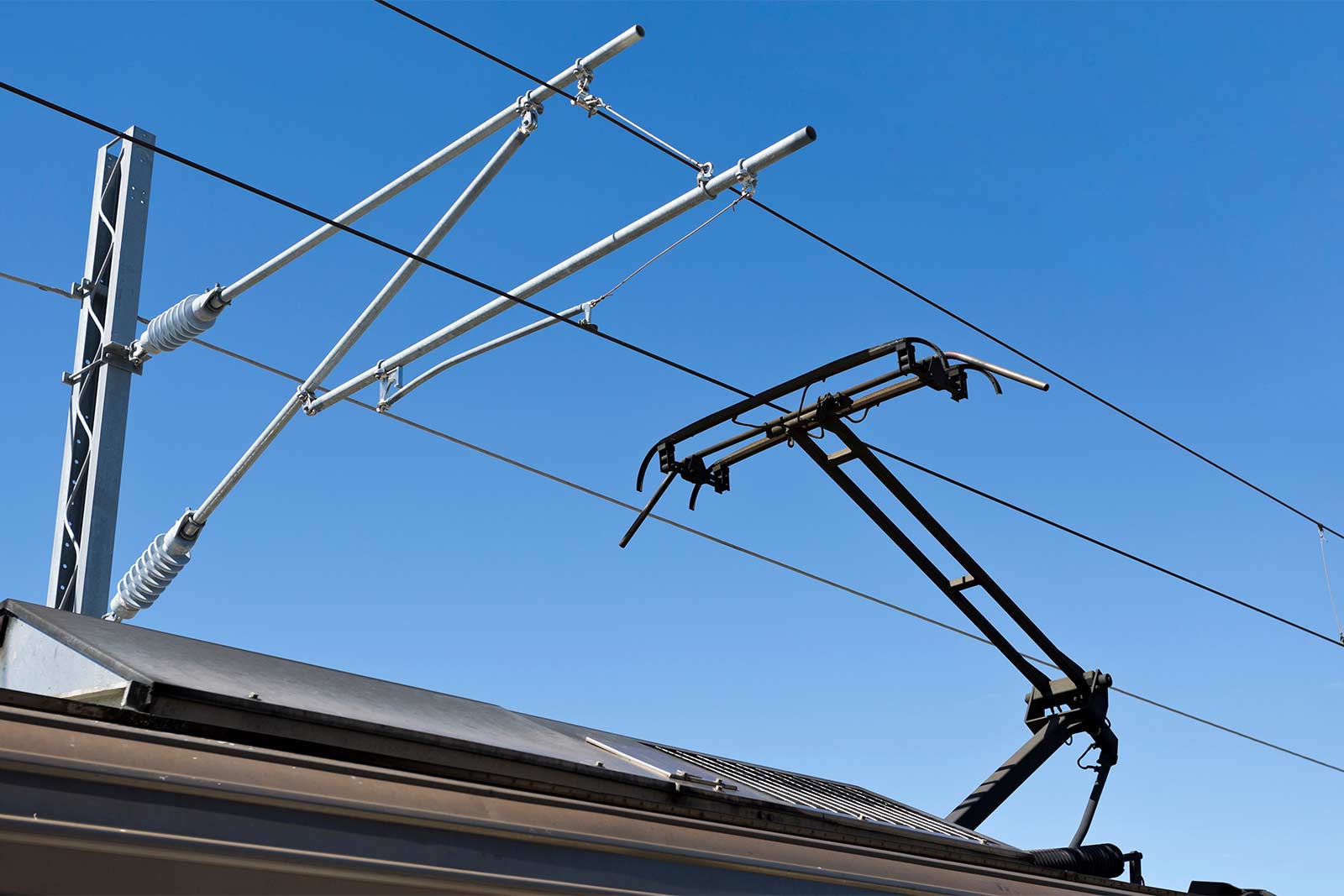
What Is the Difference Between Pantograph and Trolley Shoe Catenary Collectors?
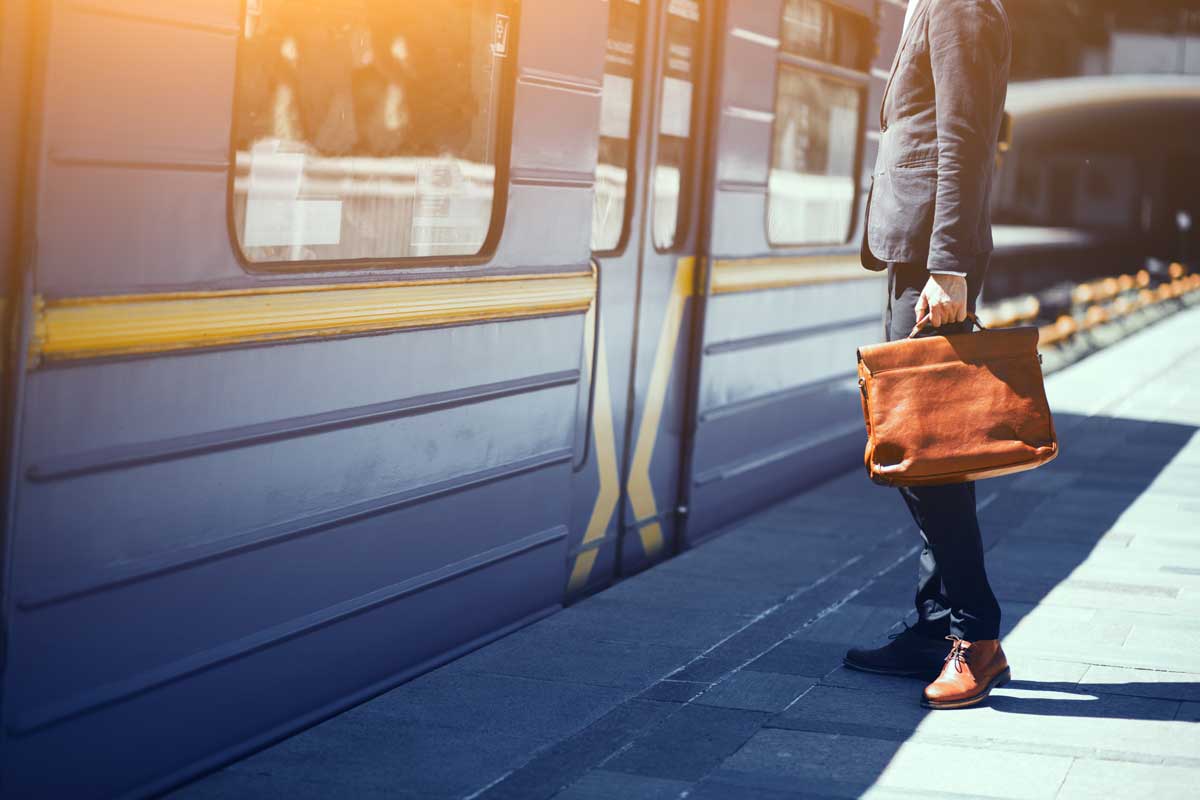