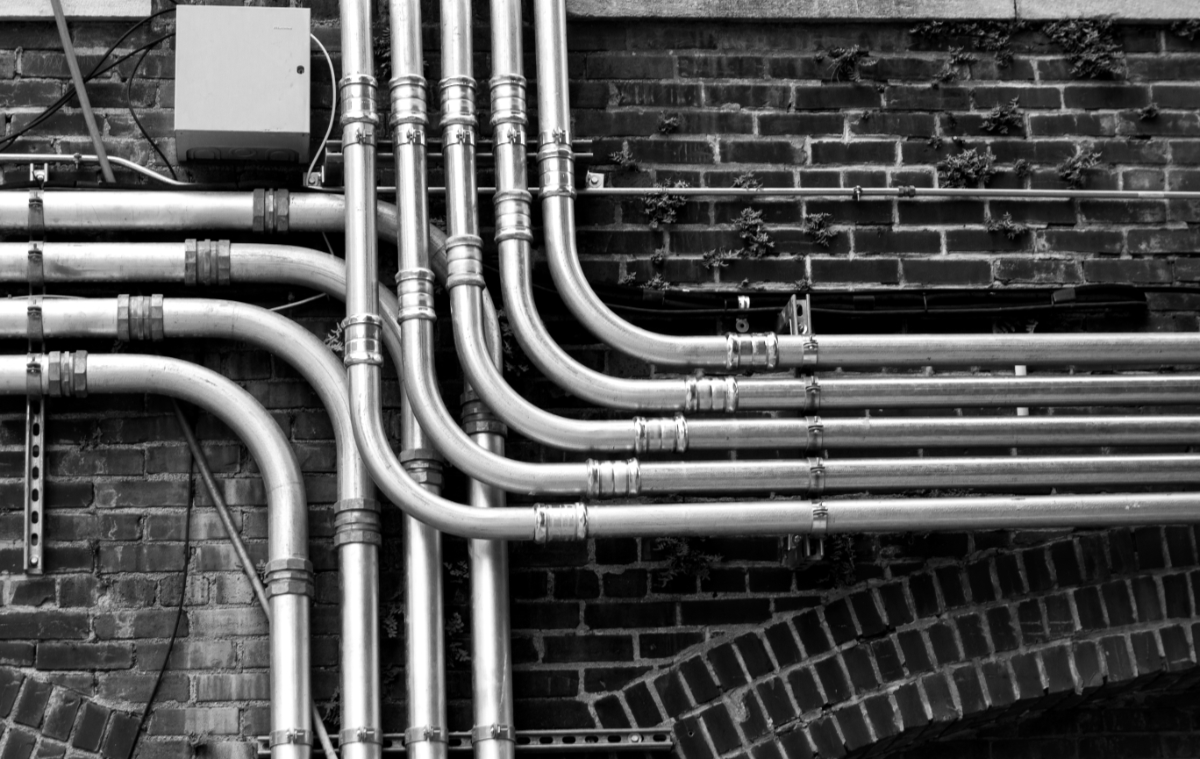
Electrical utilities play a vital role in every aspect of modern life as they generate, transmit, and distribute the electrical power we rely on daily. Grid problems or electrical power outages can cause major problems. This is why it is vital that all components of our electrical utilities systems are correctly installed and properly maintained.
Today, we will examine one important aspect of maintaining the integrity of an electrical system, ensuring that it remains secure, efficient, and safe for long-term use: conduit sealing.
Understanding Conduit Sealing
A conduit is a tube that houses, protects, and routes wiring in an electrical system. Conduit sealing involves using various materials and techniques to seal the openings of these electrical conduits to protect them against the ingress of unwanted substances, such as water, dust, gasses, and pests. The role of conduit sealing is to ensure that electrical installations remain protected and functional over long periods despite their heavy daily usage.
Moisture can cause rust and corrosion in metallic conduits and terminals, while dust and gasses can disrupt electrical connections, potentially leading to short circuits or system failures. Properly sealed conduits, therefore, ensure a secure and reliable electrical system.
Common Materials and Techniques Used for Sealing Electrical Conduits
The most common materials routinely used for sealing electrical conduits include silicone, polyurethane foam, and epoxy, as well as mechanical seals made of rubber or plastic. Depending on the application and environmental conditions, sealing can be performed using liquid sealants, injectable foam, or preformed sealing compounds.
The Importance of Conduit Sealing for Electrical Utilities
As discussed above, conduit sealing is vital in maintaining electrical systems’ integrity, safety, and functionality. In this section, we will look at key ways it achieves this.
Protection Against Environmental Elements
Water infiltration can damage electrical equipment, cause insulation breakdown, and ultimately lead to system outages. For example, unsealed conduits may allow water to enter and damage control panels during a heavy storm, leading to costly repairs and significant downtime. Sealing conduits helps to prevent such issues, particularly in the context of outdoor and underground installations.
Enhancing Safety Standards
Electrical power can be dangerous to people, property, and infrastructure if stringent safety measures are not observed. Sealing conduits reduces the risk of accidental sparks or short circuits by keeping out combustible materials, such as gasses and dust, which can ignite in the presence of electrical sparks.
Many regions have strict codes and standards that require specific sealing methods to ensure the safety and reliability of their electrical installations.
Improving System Longevity and Performance
Conduit sealing prevents electrical components from exposure to harsh environmental elements, minimizing damage to and degradation of cables and connectors. Proper sealing can dramatically extend the lifespan of the infrastructure, reducing the need for frequent repairs or replacements and ensuring consistent performance.
Preventing Corrosion and Damage
Corrosion can lead to the breakdown of metal conduits and connectors, compromising the integrity and safety of the entire electrical system. Sealing protects against corrosive elements, such as salt in coastal areas or harsh chemicals in industrial settings, and helps preserve these installations’ longevity and safety.
Common Challenges in Conduit Sealing
Proper conduit sealing is vital, but it does present some challenges. These two primary challenges personnel installing conduit sealants face center on environmental or site challenges and issues with the materials or installations.
Environmental and Site-Specific Challenges
Conduit sealing in areas with severe weather, such as high humidity, temperature fluctuations, or heavy rainfall, can present a particular challenge. Coastal areas, in particular, pose unique challenges due to salt in the air, which accelerates corrosion.
Special materials and techniques are required to ensure effective sealing in such environments. Materials used must be able to withstand the relevant conditions without degrading, so it is important to understand the various conduit sealing materials available and select the correct one for your application.
Material and Installation Issues
The type of sealant or sealing method chosen must be compatible with the environmental conditions and the type of conduit used. For example, polyvinyl chloride (PVC) conduits require different sealants than their metal counterparts.
Incorrect application of sealing materials, such as underapplying or overapplying sealants, can lead to inadequate sealing and potential failures, undermining the system’s safety and reliability. Therefore, selecting the correct material and ensuring that the seal is expertly applied is important.
Best Practices for Effective Conduit Sealing
Installing conduit sealing effectively requires training and practice. Following a few best practices is vital, and we will outline them in this section.
Select the Right Sealing Materials
Before you begin, you will need to select the most appropriate materials. Always use sealants specifically designed for electrical applications, such as silicone, polyurethane, or epoxy. Each option has unique properties and should be selected based on factors such as environmental exposure, conduit material, and application requirements.
For harsh environments, such as areas where high humidity, extreme temperatures, or chemical exposure are likely, select materials that can withstand these conditions without degrading. Next, ensure that your chosen sealant is compatible with the conduit material—whether PVC, metal, or flexible conduits—to prevent chemical reactions or ineffective adhesion.
Proper Installation Techniques
Proper installation of a conduit seal begins with surface preparation. Clean and dry the conduit surfaces thoroughly before applying your sealants, removing any dust, grease, or moisture to ensure proper adhesion.
Follow the manufacturer’s instructions for applying the sealant, ensuring you use the correct amount to create an effective barrier without overapplying, which can lead to waste or mess.
Finally, make sure that the sealant fills all gaps and voids. This prevents air pockets, which can compromise the seal’s effectiveness.
Regular Maintenance and Inspections
Properly installed conduit seals are reasonably hard-wearing. Even so, regular maintenance is important to ensure they continue to function optimally. Conduct regular inspections to check the integrity of the seals, particularly in environments prone to movement, vibration, or temperature fluctuations.
Look for signs of degradation, such as cracks, peeling, or discoloration in the sealant. These can all indicate exposure to harmful elements or simply be the effects of the system aging.
If the seal shows signs of wear or damage, reapply or replace it promptly to maintain the protective barrier.
Better Conduit Sealing With MAC Products Bushings
Our conduit sealing bushings are designed to provide a positive fluid seal for all conduits, including aluminum, rigid galvanized steel, PVC, and FRE. With a wide range of sizes and solid and split styles available, our bushings are manufactured as blank, single, two, and three conductors.
We manufacture all sealing bushings here in our on-site facility, and we also offer an installation support service to assist your team members or contractors.
If you would like to learn more about our conduit sealing bushings or anything we have covered in this post, please contact us, and we will be pleased to assist you.
Related Posts
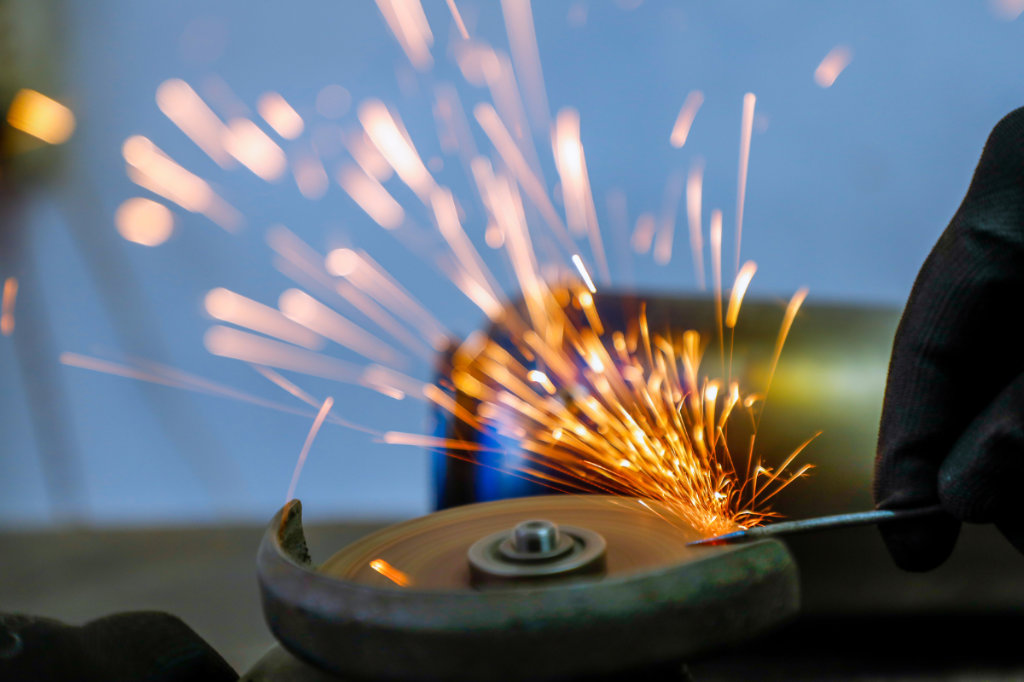
What is the Custom Fabrication Process and Why Is It Crucial for Electrical Utility and Transit Projects?
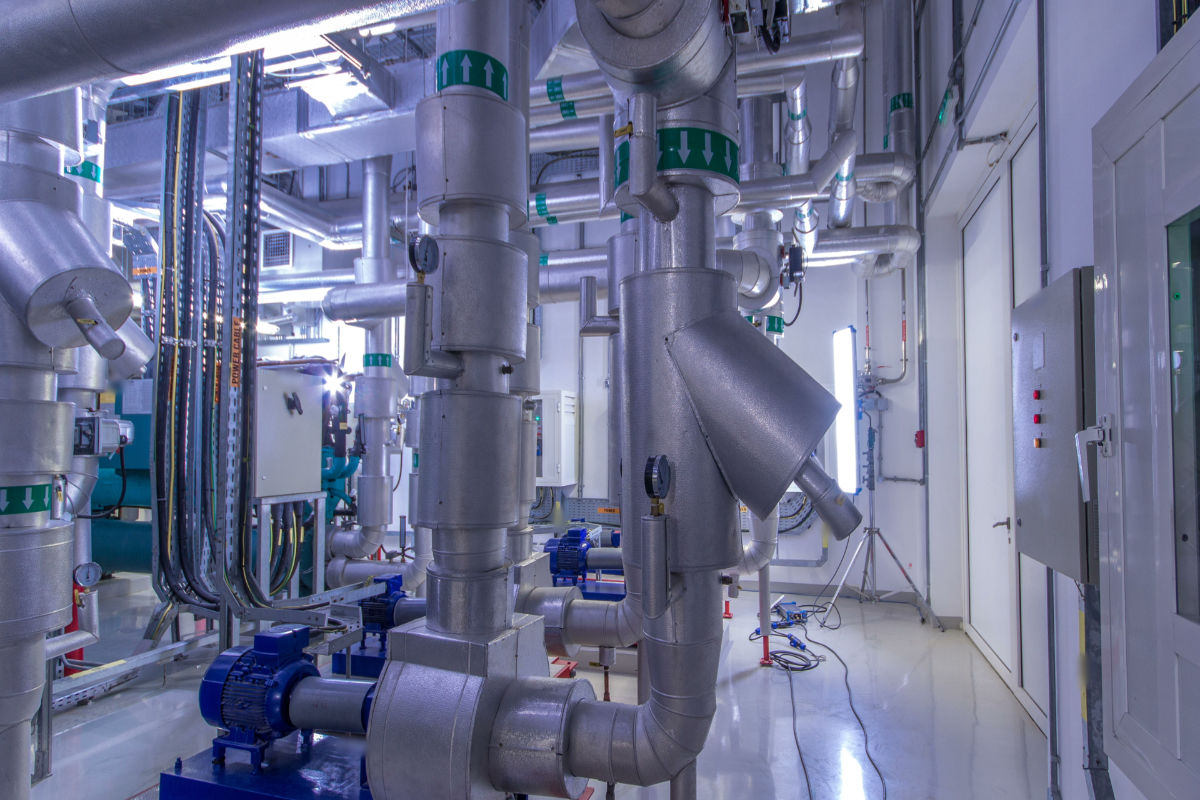
Revolutionizing Cable Cooling: Innovative Solutions for Efficiency and Sustainability in Electrical Utilities
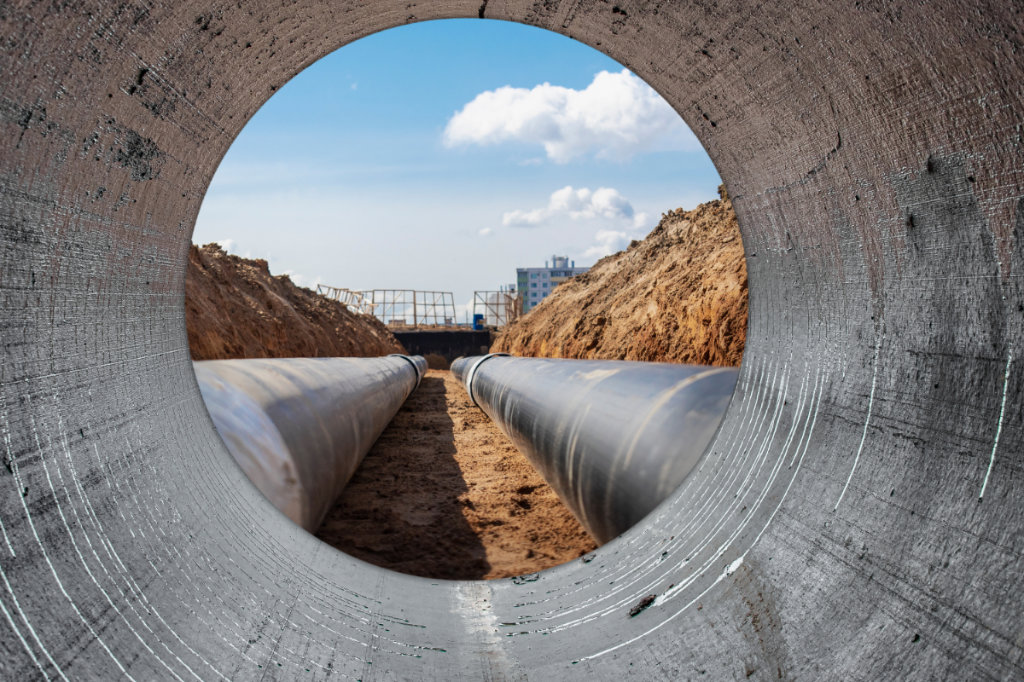